

K but are difficult to apply evenly and have the greatest risk of causing malfunction due to spillage.Metal pastes can attain thermal conductivities greater than 13 W/m The thermal formulations with the highest performance (and highest cost) consist almost entirely of liquid metal, usually a variation of the alloy Galinstan™ - a mixture of gallium, indium, and tin. However, metal-based thermal paste can be electrically conductive and capacitive and can cause malfunctions or damage if it flows onto electrical circuitry. These consist of micronized silver particles suspended in a silicone medium. If higher performance is required, silver-based compounds can have a thermal conductivity of 3 to 8 W/m
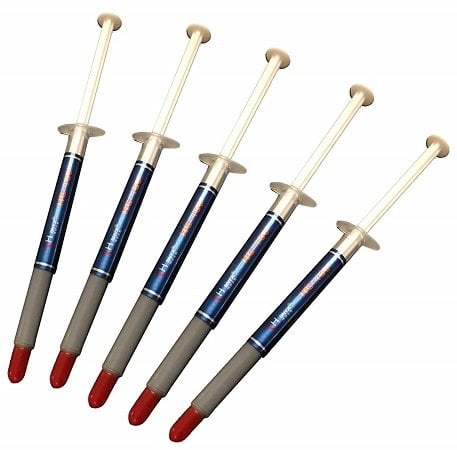
The product is electrically-insulating and non-corrosive with an operating temperature range of -40 to 200 ° C. It uses zinc oxide as the filler to achieve a thermal conductivity of 0.66 W/m Chemicals’ Type 860 is a good example of a silicon-based silicone heat transfer compound. Metal fillers tend to have higher thermal conductivities.Įach formulation is designed for a particular use case regardless, the final result must be easy to apply, fill gaps effectively, conduct heat well, and remain stable for thousands of hours without drying out or flaking. The filler content can be up to 70–80% by mass and raises the thermal conductivity of the base matrix from 0.17–0.3 W/m Fillers include carbon micro-particles, aluminum oxide, boron nitride, zinc oxide, and aluminum nitride. Typical matrix materials are epoxies, silicones, urethanes, and acrylates. Thermal paste consists of a base matrix and containing a thermally-conductive filler. Most standard thermal paste formulations are electrical insulators. Thermal paste is called by numerous names: heat sink compound thermal transfer compound thermal gel thermal grease and so on. Thermal paste is a thermally conductive compound that is applied between the heat source(s) and sink to eliminate air gaps. Any air gaps or spaces in the thermal conduction path reduce thermal efficiency and heat dissipation. Mechanically attaching the sink and source together will leave air gaps, but air is a poor conductor of heat with a λ value of about 0.025 W/m The mating surfaces between these two assemblies appear smooth to the naked eye, but manufacturing tolerances cause tiny imperfections that can clearly be seen under magnification. In a heat management design, it’s important that each stage in the conduction path is as thermally efficient as possible to maximize the heat transfer between the source and the sink. The mechanical design of a heat sink typically contains numerous fins to provide the most efficient heat dissipation within a given volume common materials for heat sinks include aluminum alloys 60, with high λ values of 166 and 201 W/m K ): it’s a measure of the material’s ability to conduct heat.The thermal conductivity of a material is denoted by λ and measured in watts per meter-kelvin (W/m The heat sink typically attaches directly to the surface of the heat source – GPU, MPU, or power device – and is constructed of a material that has a high thermal conductivity. A standard means of controlling the temperature of a semiconductor transfers the heat through conduction away from the heat source to a heat sink that dissipates it safely to the surrounding environment. Thermal paste is a key element in heat management.
